Construction Equipment Repair Costs: What You Need to Know
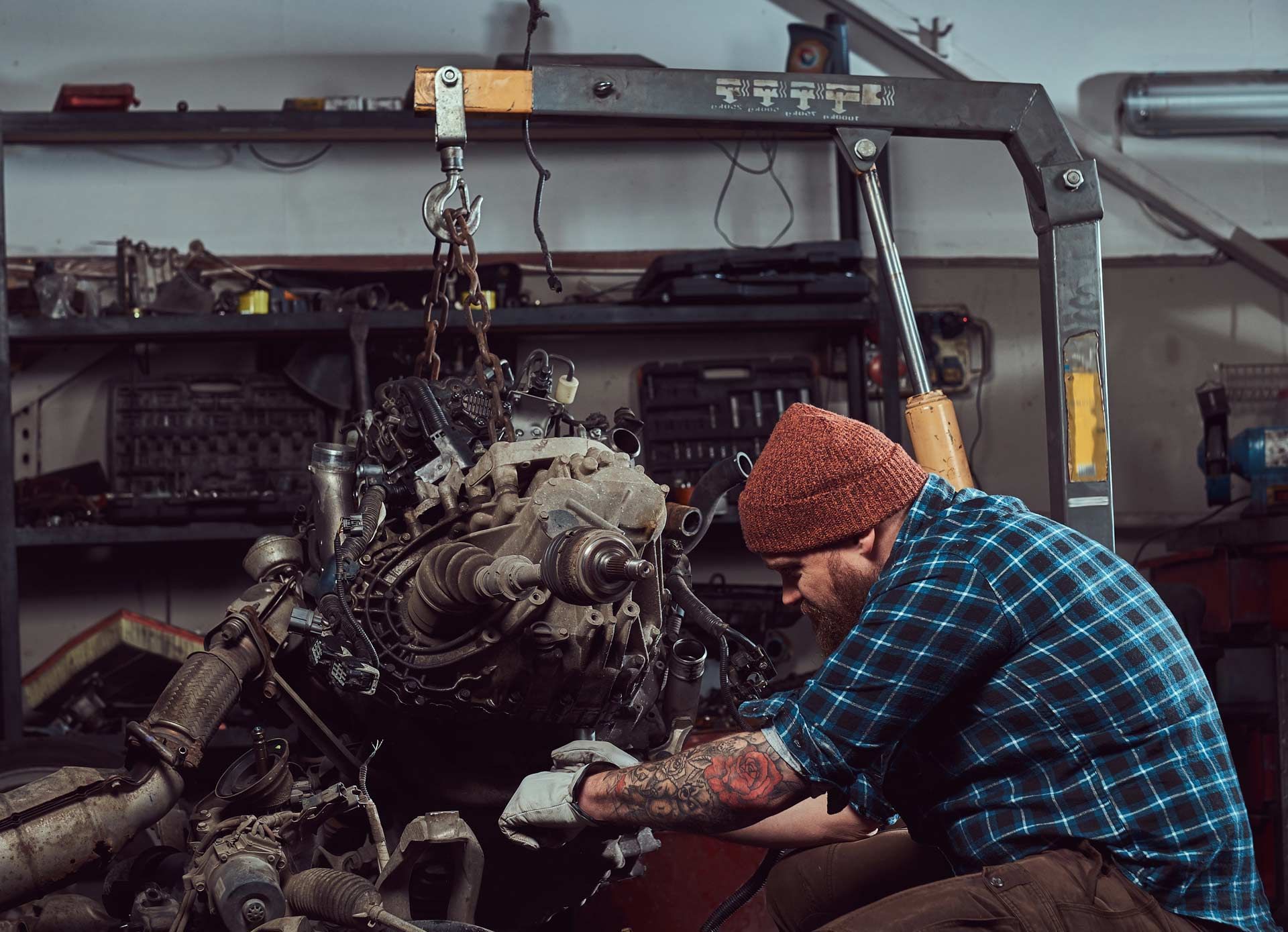
Construction Equipment Repair Costs: Complete Pricing Guide
When heavy machinery breaks down, your project timeline and budget take a hit. Equipment repairs can be costly, but knowing what to expect helps you plan better.
Construction equipment repair costs typically range from $500-$5,000 for minor repairs and $5,000-$30,000+ for major overhauls. The exact price depends on equipment type, repair complexity, parts needed, and labor rates in your area.
These costs might seem high, but they're much lower than replacing equipment. This guide breaks down repair costs by equipment type so you can budget smarter and keep your projects moving.
Understanding Construction Equipment Repair Costs
Before diving into specific costs, it's important to understand what drives repair prices. Unlike car repairs, heavy equipment service involves specialized knowledge, parts, and tools.
Factors That Affect Repair Costs
Several key factors impact how much you'll pay for equipment repairs:
- Equipment age and condition - Older machines often need more extensive work
- Part availability - Rare or discontinued parts cost more
- Repair location - On-site repairs typically cost 20-30% more than shop repairs
- Repair urgency - Rush jobs can add 25-50% to standard rates
- Labor rates - Vary by region from $75-$150+ per hour
- Diagnostic fees - Typically $150-$500 depending on equipment complexity
The biggest cost driver is often the parts themselves. For example, a hydraulic pump for an excavator might cost $1,200-$3,500 before labor.
Average Repair Costs vs. Equipment Value
A good rule of thumb in the industry is that annual maintenance and repair costs typically run about 15% of the machine's purchase price. So for a $100,000 piece of equipment, expect to budget around $15,000 yearly for upkeep.
When repair costs exceed 50% of the equipment's current value, it's often time to consider replacement instead of repair.
Construction Equipment Repair Cost Breakdown
Excavator Repair Costs
Excavators are workhorses on construction sites, and their repair costs reflect their complexity:
- Hydraulic repairs: $800-$2,500
- Engine overhaul: $8,000-$20,000
- Undercarriage repairs: $5,000-$15,000
- Electrical system: $500-$3,000
- Bucket replacement: $1,500-$5,000
Hydraulic system issues are the most common excavator problems. A blown hydraulic hose might only cost $200-$400 to fix, while a failed hydraulic pump could run $2,000-$3,500 including labor.
Bulldozer Repair Costs
Bulldozers take serious abuse on jobsites, leading to these typical repair expenses:
- Track replacement: $4,000-$12,000
- Transmission repairs: $5,000-$20,000
- Blade repairs/replacement: $2,000-$8,000
- Engine repairs: $2,500-$15,000
- Hydraulic system: $1,000-$5,000
Track maintenance is critical for bulldozers. Rebuilding undercarriage components costs $8,000-$15,000 for medium-sized dozers, representing about 50% of lifetime maintenance costs.
Crane and Backhoe Repair Costs
These versatile machines have their own repair cost profiles:
Cranes:
- Hydraulic cylinder repairs: $1,500-$5,000
- Cable/wire rope replacement: $2,000-$10,000
- Outrigger repairs: $1,000-$4,000
- Control system issues: $1,500-$7,500
Backhoes:
- Loader arm repairs: $1,200-$3,500
- Stabilizer repairs: $800-$2,000
- Hydraulic system: $1,000-$4,000
- Drivetrain issues: $2,500-$7,500
Asphalt Paver Repair Expenses
Asphalt pavers have specialized components that can be costly to repair:
- Screed repairs: $2,000-$8,000
- Conveyor system: $1,500-$4,500
- Hydraulic system: $1,200-$5,000
- Heating element replacement: $800-$3,000
The screed system is particularly crucial - when it fails, production stops completely. Regular maintenance can prevent major screed repairs that typically cost $3,000-$8,000.
Forestry Equipment Repair Costs
Feller Buncher and Skidder Repair Pricing
Forestry equipment operates in harsh conditions, leading to unique repair needs:
Feller Bunchers:
- Saw head repairs: $3,000-$15,000
- Hydraulic system: $2,000-$7,000
- Boom repairs: $2,500-$8,000
- Grapple repairs: $1,800-$5,000
Skidders:
- Tire replacement: $2,500-$6,000 per tire
- Winch repairs: $1,500-$5,000
- Grapple repairs: $2,000-$6,000
- Transmission work: $5,000-$18,000
Mulcher and Forwarder Repair Expenses
These specialized machines have their own repair profiles:
Mulchers:
- Cutting drum/teeth: $2,000-$8,000
- Drive system: $3,000-$12,000
- Hydraulic repairs: $1,500-$6,000
Forwarders:
- Crane repairs: $2,500-$10,000
- Bunk/grapple system: $2,000-$7,000
- Transmission/drive: $5,000-$20,000
Harvester Maintenance Costs
Harvesters combine multiple functions with corresponding repair costs:
- Harvester head repairs: $4,000-$20,000
- Boom repairs: $3,000-$9,000
- Measuring/control system: $2,000-$7,500
- Hydraulic system: $2,500-$8,000
The cutting components alone on a harvester head can cost $1,500-$4,000 to replace, not including labor.
Truck Repair Cost Analysis
Dump Truck and Flatbed Repair Expenses
Heavy-duty trucks face different repair issues than off-road equipment:
Dump Trucks:
- Hydraulic lift system: $1,200-$4,500
- Body repairs: $2,000-$7,000
- Suspension work: $1,500-$5,000
- Brake system overhaul: $1,000-$3,000
Flatbeds:
- Deck repairs/replacement: $2,000-$8,000
- Hydraulic system (if equipped): $800-$3,000
- Suspension repairs: $1,200-$4,000
Specialized Truck Repair Costs
Purpose-built trucks have unique components that affect repair costs:
Tankers:
- Tank repairs: $3,000-$15,000
- Pumping system: $1,500-$5,000
- Valve/plumbing repairs: $800-$3,000
Logging Trucks:
- Loader repairs: $2,500-$8,000
- Bunk system: $1,800-$5,000
- Frame reinforcement: $2,000-$6,000
Refrigerated Trucks:
- Cooling system repairs: $1,800-$7,000
- Insulation/box repairs: $2,000-$8,000
- Generator/power system: $1,500-$5,000
Diesel Engine Repair Pricing
Diesel engines power most heavy equipment, with common repair costs including:
- Injector replacement: $250-$400 per injector
- Turbocharger repairs: $1,500-$4,000
- Head gasket replacement: $2,500-$6,000
- Complete engine rebuild: $15,000-$40,000
- Emissions system repairs: $1,000-$7,500
Newer engines with advanced emissions systems often cost more to repair than older models due to complex electronic components.
Agricultural Equipment Repair Expenses
Tractor and Combine Harvester Repair Costs
Farm equipment faces seasonal demands and specialized repair needs:
Tractors:
- Transmission repairs: $3,000-$12,000
- Hydraulic system: $1,200-$5,000
- PTO repairs: $800-$3,000
- Clutch replacement: $1,500-$4,000
Combine Harvesters:
- Header repairs: $2,000-$10,000
- Threshing mechanism: $3,000-$15,000
- Cleaning system: $2,500-$8,000
- Drive system: $4,000-$12,000
Farm Implement Repair Pricing
Implements need their own maintenance budgets:
Plows:
- Share/point replacement: $50-$200 per piece
- Frame repairs: $500-$2,000
Balers:
- Pickup mechanism: $1,200-$4,000
- Bale chamber repairs: $2,000-$7,000
- Knotting/wrapping system: $1,500-$5,000
Seeders:
- Meter repairs: $800-$3,000
- Opener repairs: $500-$2,000
- Drive system: $1,000-$3,500
Seasonal Maintenance Expenses
Planning for regular seasonal maintenance helps prevent major breakdowns:
- Pre-season inspection: $300-$1,000
- Post-season winterizing: $200-$800
- Fluid and filter changes: $200-$800
- Calibration services: $300-$1,200
Many farmers find that spending $2,000-$5,000 annually on preventative maintenance saves $10,000-$20,000 in emergency repair costs.
How to Reduce Equipment Repair Costs
Preventative Maintenance Strategies
The most effective way to cut repair costs is preventing problems:
- Follow manufacturer schedules for all maintenance
- Train operators to spot early warning signs
- Keep detailed maintenance records for each machine
- Perform daily inspections before operation
- Use high-quality fluids and filters
Investing in operator training can reduce repair costs by 25-40% by preventing abuse and catching issues early.
When to Repair vs. Replace Equipment
Making smart repair decisions requires analyzing several factors:
- Compare repair cost to current equipment value
- Consider downtime costs during extended repairs
- Factor in reliability after repairs
- Analyze fuel efficiency of old vs. new equipment
- Calculate productivity differences between repaired and new machines
When repair costs exceed 50-60% of the equipment's value, replacement usually makes more financial sense.
Finding Reliable Repair Services
Not all repair shops offer the same quality:
- Research reputation and experience with your equipment type
- Ask about technician certifications and training
- Check warranty policies on parts and labor
- Compare diagnostic fees and hourly rates
- Look for preventative maintenance programs
A quality repair provider might charge more per hour but complete work faster and more effectively, reducing total cost.
Maximizing Equipment Longevity While Minimizing Costs
Managing equipment repair costs requires balance. Regular maintenance prevents costly breakdowns, while knowing when to repair versus replace saves money long-term.
Remember that proper operation, timely repairs, and scheduled maintenance all work together to extend equipment life. By understanding typical repair costs, you can budget accordingly and make informed decisions.
Ready to Keep Your Equipment Running at Peak Performance?
Don't let equipment downtime drain your profits. Tree Top Equipment Repair specializes in construction, forestry, truck, and agricultural equipment maintenance with expert technicians and competitive rates.
Our precision diagnostics and rapid turnaround ensure your machinery gets back to work quickly. From hydraulic services to complete engine rebuilds, we handle it all with quality parts and guaranteed workmanship.
Contact Tree Top Equipment Repair today for a free assessment and discover how our preventative maintenance programs can reduce your repair costs while maximizing equipment lifespan.